Printing an Infinite Future
By Audrey Robinson | Junior Designer
Workplace interiors are generally renovated every five to seven years, sometimes faster, perpetuating a steady stream of waste products that for the most part make their way into landfills and require the production of new products to take their place. Next to the use of concrete and steel, this process is one of the most environmentally damaging scenarios in the AEC sector.
Overall, the building industry is responsible for 33% of the world’s waste and 42% of all global CO2 emissions. Reducing these numbers via a circular economy for the built environment is critical but how do we make that happen?
Pursuing that question as the recipient of an IA Spark Fellowship, I recently flew to the Netherlands to explore a technology that is and will be a huge contributor to realizing a circular economy and the level of sustainability critical to the health of the planet.
In Amsterdam, I visited and worked with Aectual, a leading manufacturer of materials, finishes, and furniture made from recycled waste streams and plant-based materials—typically recycled drink cartons (PolyAL), recycled Bio-PA, and wood waste. When an Aectual product is no longer needed by a client, the company takes it back and shreds it into materials for the creation of entirely new and different products. With this flexible process, materials become one thing for any number of years and then become something else with a new life and purpose. Aectual’s circular materials loop, supported by a no-waste manufacturing process based on a network of extra-large robotic 3D printers and recycling partners, can continue indefinitely for the same client or different clients or agendas. And, as a plus, a digital materials passport is generated for each of the recycled materials verifying their characteristics for reuse in a circular economy.
Aectual works with clients to design and create customized products from its standard recycled materials or from client-provided waste material. For example, the company collaborated with Lenovo transforming e-waste into functional furniture. They also offer a catalog of systems from recycled materials that include wall panels, acoustic panels, screens, furniture, flooring, lighting, and more. These products are as functional as they are aesthetic. Wall panel solutions, for example, provide a sound reduction of 50%-85%. In addition, a variety of screen systems that hang from the ceiling or attach to glazing are available.
While not well known in the U.S., robotic 3D printing is widely used in Europe. Although the US is behind in this technology, Aectual is aiming to open a U.S. production hub hopefully in the fourth quarter of this year. As designers, we will have the opportunity to be at the front of 3D printing for interior design in the U.S.

Aectual | Pixel Brick Screen
Hands on Research
While there I interviewed Aectual Creative Director and Co-founder Hedwig Heinsman, who was gracious and generous with her time.
For a hands-on perspective, I designed and created a project with the guidance of Sven de Haan, who specializes in the emerging field of parametric design and digital fabrication combining a knowledge of programming, fabrication processes, and architectural design. To test the limits of the Aectual printer my design focused on the geometry rather than the function of the 3D model I wanted to create. My inspiration was the beautiful, complex mycelium networks found beneath the forest floors of the Pacific Northwest.
For the design process, Aectual uses Rhinoceros, a commercial 3D computer graphics software that I have worked with before. After I constructed my design we streamlined it to a single three-foot by three-foot panel with three different structural levels. Filament layers were mapped to make sure each ribbon of filament would have the proper support. This 20-second time-lapse captures about 3 hours of print time focused on one level. Together the three levels took about 10 hours to print. With more time for development, the final result could easily become functional as a desk screen, wall panel, or decorative architectural element.
Outcomes
The process of creating new products from existing sustainable materials with no harm to the environment, as well as verifying and recording the composition of the materials for future use, is an elegant proposition with almost unlimited potential—one of many needed to implement a circular solution. Today’s chairs might become tomorrow’s reception desk or decorative cladding to enhance an interior or exterior wall.
My research at Aectual directly aligns with IA’s goals for sustainability and the sustainable objectives of our clients. As a result of my fellowship, IA and Aectual are currently in the process of exploring a pilot project for one of our large tech clients. Since it is estimated that the adoption of this type of circular process could reduce the amount of waste we produce by almost 60% in five years, I am excited and hopeful. This is a possibility well worth exploring. With the rapidly increasing climate crisis, it is the responsibility of designers to identify every opportunity and innovative means to reduce global warming, champion sustainability, and support the circular economy.
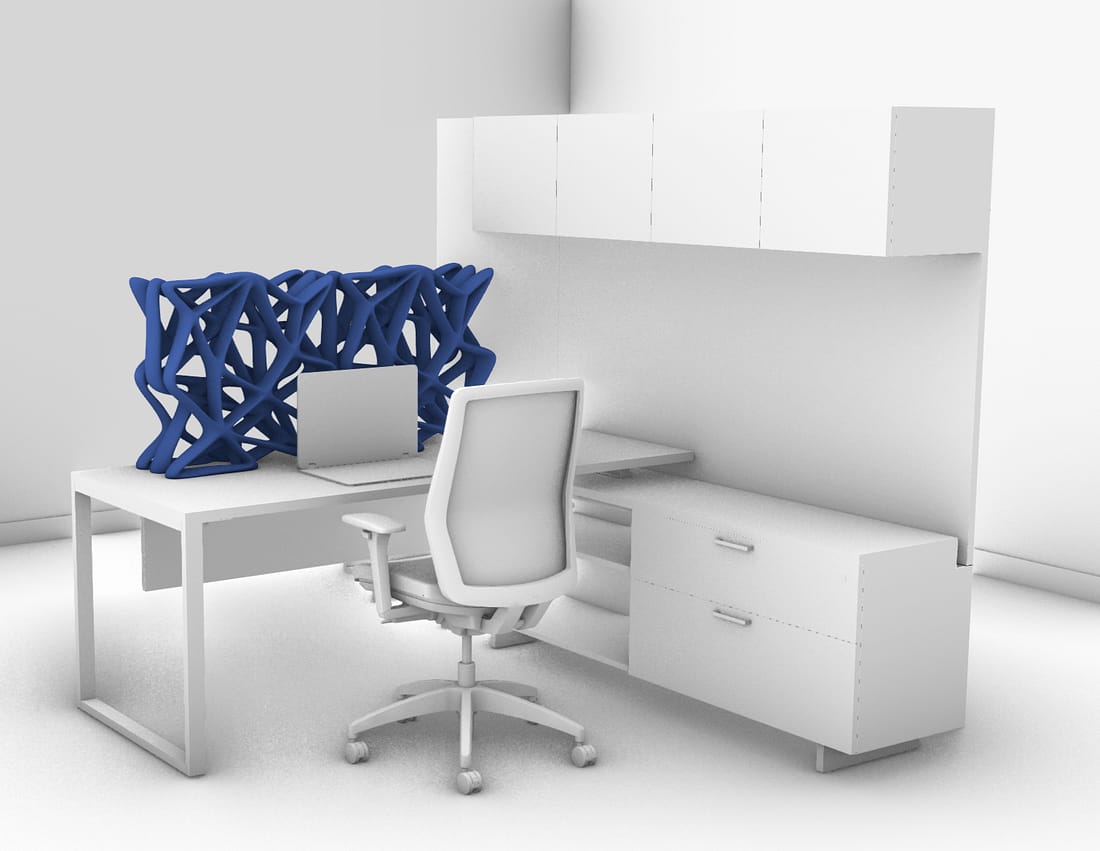
A sample 3D-printed screen designed by Audrey Robinson