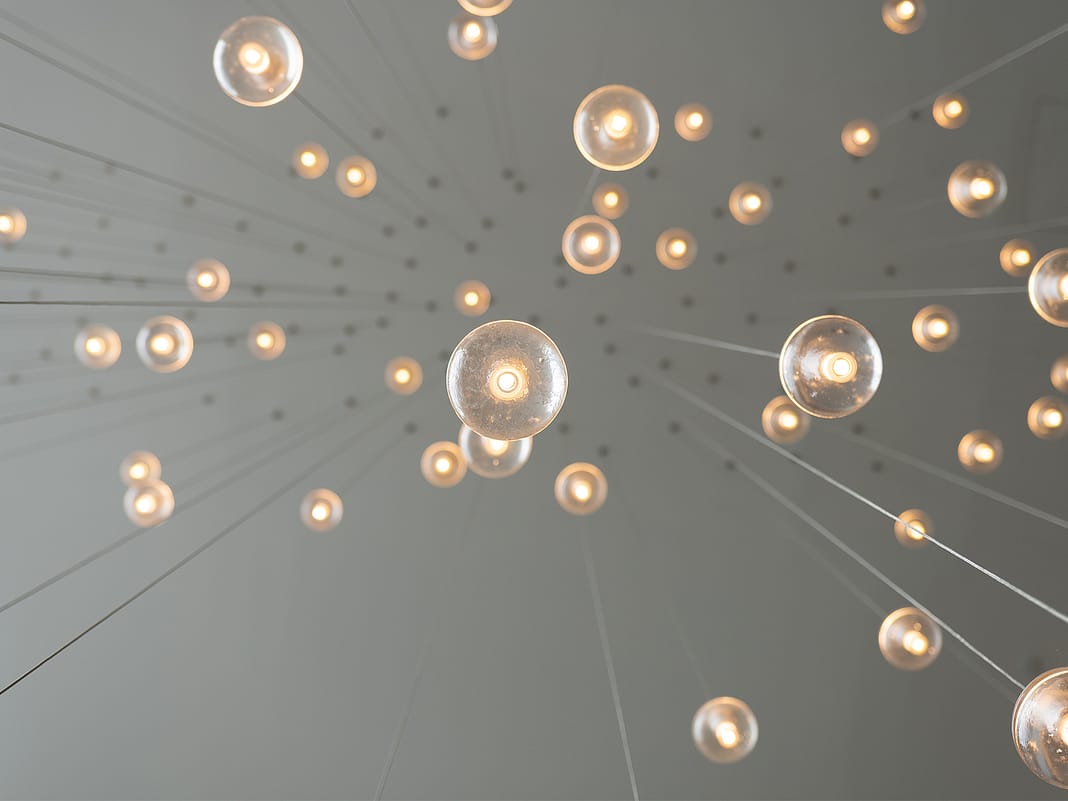
By Gary Bouthillette, AIA, NCARB, LC | Senior Director of Lighting Design
As global supply chain shortages escalate, the impact on the availability of commercial lighting fixtures is no exception; some fixtures will be affected well into 2022. How bad is it? Lead times that used to be two to four weeks may now be six to eight weeks, with the suspension of many quick-ship programs. To guard against hoarding one major manufacturer of LED drivers is even requiring confirmed orders for projects before shipping components to fixture fabricators. To ensure the integrity and timeliness of their designs, how are lighting designers navigating this scenario?
In general, for a variety of reasons lighting fixtures are especially prone to supply chain disruptions. With the advent of LEDs, lighting is now squarely a tech industry, dependent on a steady supply of chips and other high-tech components similar to consumer electronics and the auto industry, which has seen entire plants shut down due to electronics shortages. Some types of chips used in lighting fixtures are only manufactured at a few overseas plants and are particularly susceptible to labor shortages and shipping delays.
Surprisingly, lighting fixtures contain a wider variety of materials than most other building components. Drywall and carpet, for instance, require few materials compared to a lighting fixture, which may contain steel, plastics, aluminum extrusions, paint and other coatings, electronic assemblies, wiring, and LEDs. A shortage of any of these components can easily disrupt a factory’s ability to get product out the door. But as designers we have options—working with manufacturers, avoiding high-risk specifications, remaining flexible, and early ordering—to ensure the functionality, aesthetics, and timeliness of lighting designs.
Talking to Manufacturers
Discussing anticipated lead-times with potential manufacturers before specifying their fixtures, regardless of positive past performance, is vital to avoid the need for last-minute alternates with shorter lead-times that might not have a good value-to-cost ratio for the client. If possible, we meet with the sales representative and a direct representative of the factory to understand current production capacity, delivery capabilities, and strategies for avoiding supply chain issues. What has the typical lead-time been on recent orders the size of ours? Are they having any issues sourcing LED drivers or other components; are they experiencing any major shipping delays?
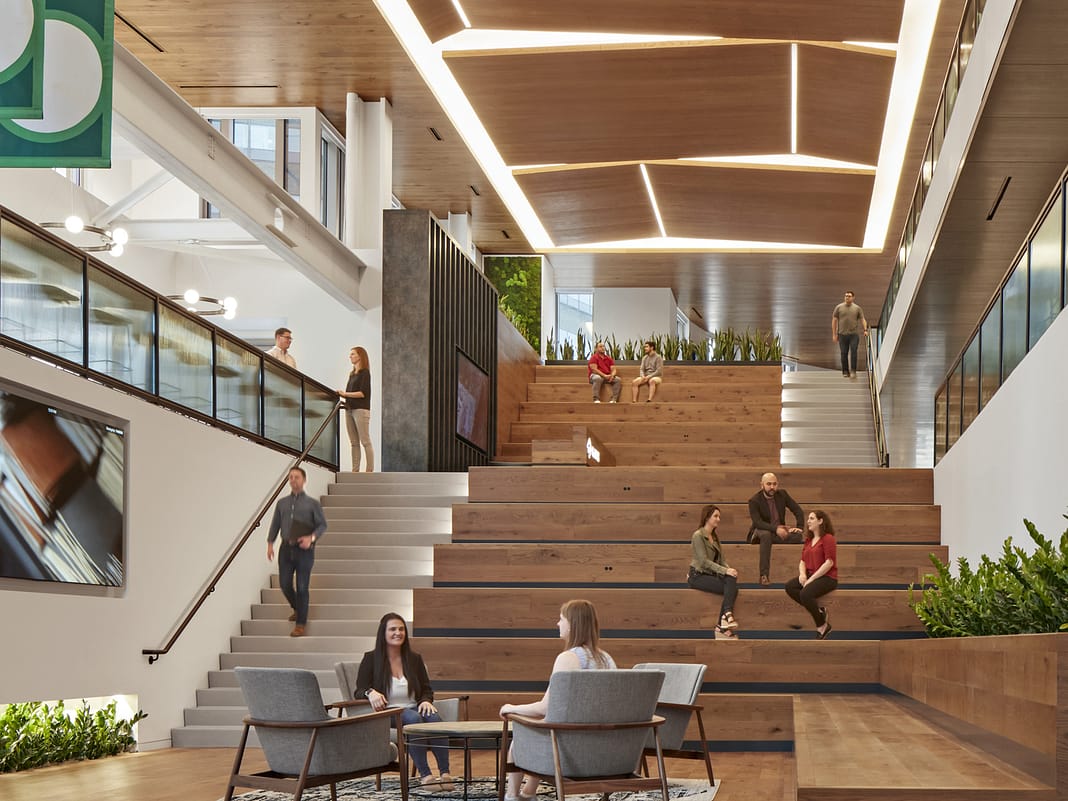
Confidential Client, Boston. Photography © Robert Benson.
Avoiding high-risk specs
We know that some decorative lighting lead-times have increased from 10 to 12 to 24 weeks or more! There is no point in considering specifications that have no chance of meeting the project schedule. Realistically, we do not rely too heavily on any one particular lighting fixture. If the construction schedule is tight, we are cautious about products that may need to ship from overseas after fabrication.
Flexibility
We consider alternative features or other light fixture types to reduce lead-times. Our most common request is for a substitution of LED drivers due to specific supply shortages. Substitutions are vetted to ensure controls compatibility and to verify that functionality will be the same as the original product specified. We are open to considering changes suggested by subcontractors and distributors, but will independently validate any proposed options.
Ordering Early
If our construction schedule can’t accommodate several weeks of additional lighting lead-time, we consider releasing the lighting package early. As lighting designers we don’t like to do that because later design revisions could trigger lighting changes after release. However, this may be the only way to mitigate the greater risk of late fixture deliveries delaying a client’s move-in.
Conclusion
The supply chain for lighting fixtures and components may now be tighter, but through forethought, vision, and expertise they will remain elements of a design solution functionally and aesthetically on track, delivered on budget and on time without compromising creativity or sustainability.